不断改善,取得成功
康美(ConMed)是一家全球的医疗结束公司,专注于医疗产品的开发,制造和销售,这些产品帮助内科医生为患者提供优质的护理服务,增加临床效果。康美公司也是世界著名的外科手术医疗器械和仪器制造的领导企业。
康美公司通过战略并购的方式取得了巨大的成功。传统方法,公司将获得的产品线原封不动的转移到自己的工厂。因此,康美公司层继承了许多效率低下并存在严重浪费的制造流程。康美公司最终不得不依靠剧的的在制品库存,低下的生产效率和过高的安全库存来保证对客户的及时交货。
以消除浪费和提高效率为重点的改善刻不容缓。康美公司将精益之旅作为业务增长,提高服务水平和为员工及股东增加收益的首选模式。
从哪里开始?
许多公司采用的标准方法是从制造环节开始推展精益,一旦实现了卓越运营,再扩大到其他区域。然而,近些年一些公司开始采取一种更快的方法,他们意识到,如果从最初就深挖改善机会,那么将会有更大的成效。
但是这种方法需要公司有坚定的信念和对改善所做努力的承诺。按照康美公司COO Dave Johnson的说法,精益的实施需要从上至下推进,但是有需要从下至上执行。
他补充道,我跟他们说,这不是一个项目,而是一场文化的变革。
如果你真的想那么做,那么你必须得到高层支持,
说到做到,每天每周到生产现场参与改善。
Johnson的另一个经验教训是从一开始便整合财务部门,如果没有他们的介入,很难展示改善的成效。他们可以提供报告,从不同的层级到不同的生产线,区分改善的生产线和未改善的效果。我们发现,改善的生产线可以有高达20%的效率提升。
另一个经验教训是许多公司未能结合财务指标和报告来发现精益的效果。简明扼要的财务报告可以抓出生产,材料,劳动力等各方面的区别。Johnson阐述,虽然精益的开始听起来很简单,但很多公司做的并不好,只是建立一个精益团队,但是缺乏有效的手段和方法。我们的理念是将远景展示给员工。每天早上巡视工厂可以创造有效的可视化效果,使员工负起责任。使精益之旅有一个良好的开端。
明显的成效
在TBM的帮助下,在第一年,康美完成了33项改善活动,其中包括23项生产现场改善活动,6项快速换模活动,3项流程改善活动,一项日常管理活动(MDI)。公司也为这些活动设定了目标,并达到了超出目标的结果
- 生产效率提升22% (目标为20%)
- 占地面积缩减66% (目标为40%)
- 在制品减少85% (目标为75%)
- 通过改善活动,38名经验丰富的员工被安排到新的项目中,
面积和人工的减少帮助康美公司实现了最少200万美元的节约,更重要的,这些资源可以用于新的生产和产品线,增加收益。
可视化管理和责任心
责任和担当是精益管理的重要因素之一,有效的可视化管理可以推动责任心。康美公司建立了一整套的先进的可视化系统,其中包括用于异常管理的安灯,以及向不同负责对象传递信息的电子信息系统。而且这些安灯的设置是经过特殊定制,更有效的针对康美的现场情况作出的改善。
关键要素
康美公司采取了积极多元的方法实现精益变革。这绝非一项简单的任务,但是结果表明,这一切的努力都是值得的。Johnson指出,在这期间他认识到,如果你没有衡量指标就没有改善,不存在负责或者执行,只是在练习。这也是大多数公司失败的原因,因为他们无法衡量,无法作出解释及行动。
很多公司将精益是为一个降低成本的机会,但是在康美,他们将此视为一个增长策略。从客户的角度出发,观察流程中的改善机会。这是一个理念的差别。
康美公司既不缺乏领导的力又不缺乏承诺,结合明确的目标,纪律和责任心,康美公司成功的找到了他们成功所需的各类因素。更快速的响应客户,实现突破性的增长。
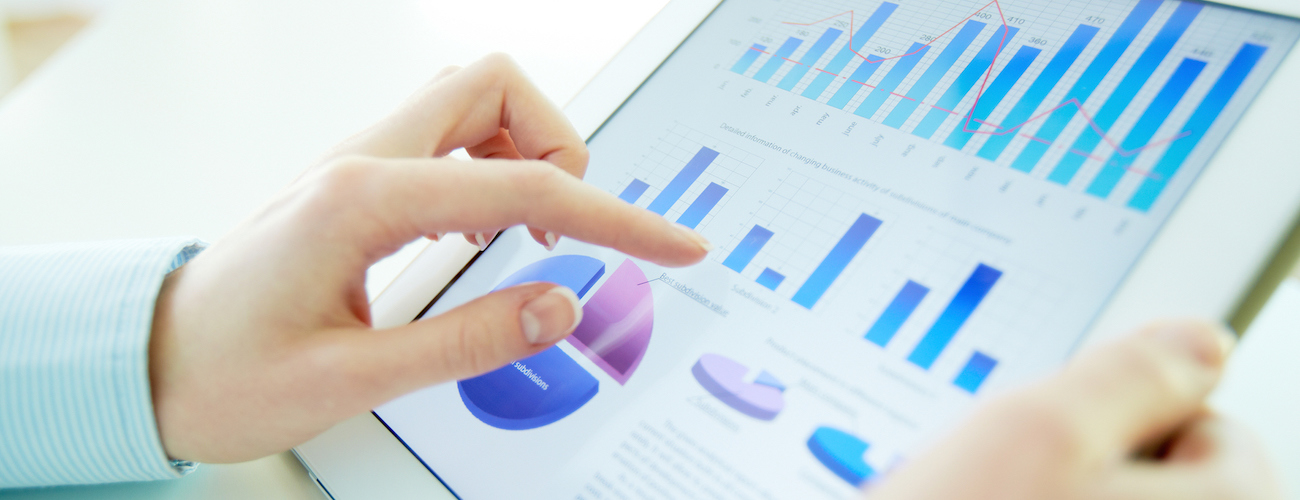
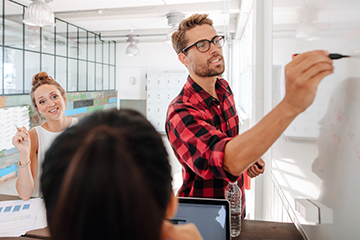