客户为中国一家著名的轨道机车生产企业,乃是国家“一五”重点建设项目之一。拥有员工超过一万人,旗下还同时拥有多家全资子公司和控股子公司,及合资企业与境外参股企业。该客户产品覆盖全国所有的铁路局;约占全国运营车辆的50%。经过50多年的建设和发展,已经成为生产规模、装备水平、研发能力世界一流的高速车、城铁车和转向架的研发、制造、检修和出口基地。
该企业于2010年在集团总公司的方针策略的号召下率先开始推行精益管理,在与TBM的共同合作努力下,该客户的精益推行工作取得了长足的进步,尤其是制造系统和设计领域,通过持续的系列改善活动的开展,逐步营造了全员参与精益的文化氛围,并构建起了全公司从上到下推动,管理,评价改善的运行机制,公司整体运营指标在安全,质量,交期(包括制造周期的缩短)方面体现出改善趋势。
职能部门已逐步在提升起服务内部客户的意识,并开始建立起支持生产系统精益的精益子系统。为精益管理体系的确立和运行,内部顺畅沟通机制的形成,和根据企业方针形成组织执行能力确立了重要基础。
精益管理历程 (2010 - 2014)
现场改善活动实例
加工生产线的拉动系统建立
–改善目标:该次改善活动基于内饰件加工线与下工序装配之间成品居高不下,且加工批量为按列投产,加工批量大且不同步。
–改善进程:改善团队首先核算了瓶颈工序-表明现有批量可以减少一半且不损失产能。团队运用货店超市原理建立成品超市, 以及运用看板来传递成品被下序取走的信息,生产开工指令,和完工入超市的信息,并将该信息展示于看板管理板上。改善团队在改善周内制作了简易的看板和管理板进行了模拟运行;
–改善效果: 正式运行后成品区的库存两较改善前降低了25%, 半成品降低了60%, 且信息的传递更加一目了然。
创建流程标准化生产线
–改善目标:诸多项目的诸多零件工艺相似,但物流路线长且散乱,布局不合理,在制品高等现状问题;
–改善进程:首先改善团队选取了四个车型的,3300多种料件进行产品品种-数量分析,识别数量占80%的20%种类的料件570多种,通过运用流程标准化图表对该570多种料件进行分组与简化,并整理出两条主要工艺路线。通过产能分析,核算出其所需要的人员和设备;
电气设计平台改善
–该改善活动主要通过该平台将电气系统接口标准化,且改善工艺性,可用性,和可维护性,缩短装配,调试周期。
–由业务,开发,采购,生产,质量等跨部门成员组成的改善团队首先学习了关于精益西格玛设计的原理和改善方法,通过集思广益梳理出原有设计中出现过的问题,分析在新的开发项目中的潜在的失效问题。团队分成小组,针对平台的各类接口,到装配现场就工艺性,质量,可维护性一一听取一线人员的意见反馈。
–各小组就各类接口提出多选替换方案,并对各替换方案进行优缺点分析和量化评价,优选出最佳的方案。
–团队在改善活动中总结出各个接口存在的潜在问题和改进方案,并对这些方案进行了分析,优化,制定 出适合B型车的标准化设计指导最佳方案,新方案实施后电气设备的安装操作性和可维护性比改进前提高42%。
–改善效果:方案实施后,料件的流转周期缩短了32%,在制品降低20%。
推进精益后公司综合运营指标改进
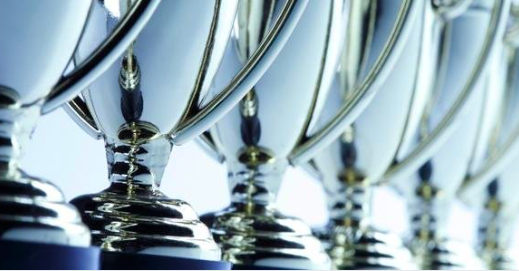
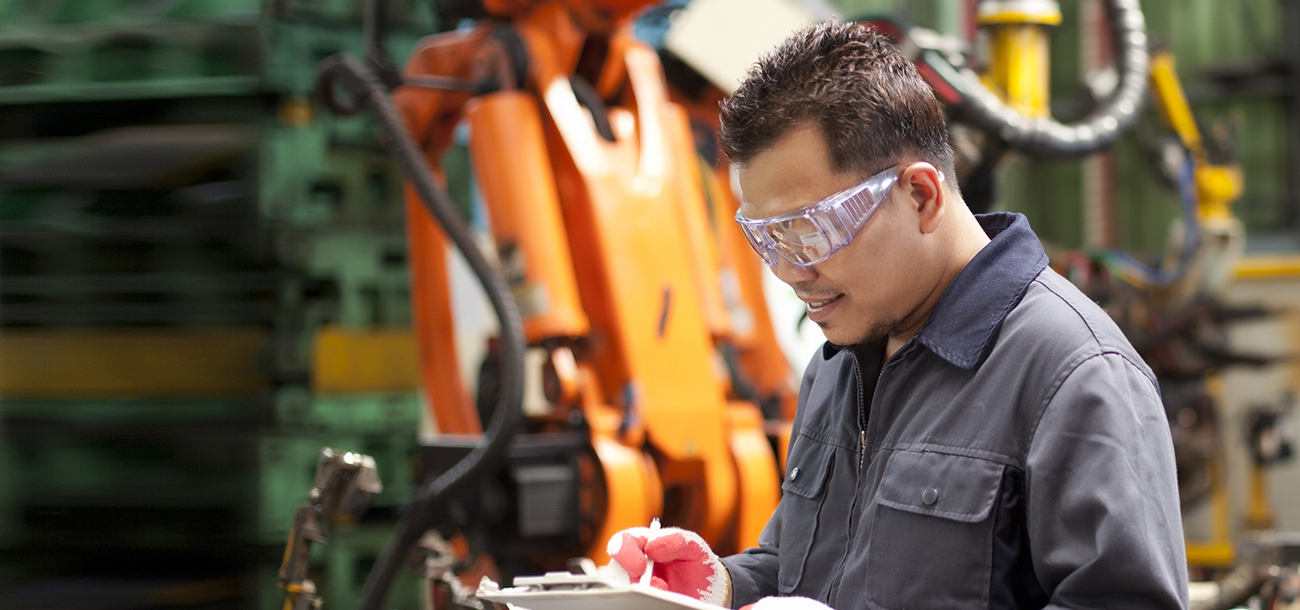