任何行业的快速增长都令人兴奋并附有挑战。在运营角度讲,效率增长和产出的提升可以提高收益,并延缓现金的资本支出。
在过去几年中,TBM咨询集团帮助这家快速增长的食品制造商实施业务改善计划。 本案例研究详细介绍了此项目,展示了该项目如何加强了公司的收入和EBITDA的增长,并强调了文化变革和有效的管理体系对卓越运营的重要性。
大量的挑战
该公司的股东,一家私募股权投资公司,要求TBM顾问介入并帮助旗下公司提高经营业绩。 我们的工作集中在两个分部。 这两家工厂位于城市的远郊,员工希望为公司的成功作出贡献。
每个工厂分为两个主要区域:生产和包装。 包装进一步细分为三个区域:调味,灌装和最终包装。 由于生产过程具有强制性的“清洁到位”要求,迫使设备定期关闭进行卫生清洁。 清洁过程将最大潜在效率降至85%左右。
两家工厂的管理人员都在使用各种管理工具——粗略的价值流图,标准作业和5S作为持续改进的基础。尽管很努力,但人员存在经验有限,训练不足的缺陷。由于产品对温度的敏感和易腐烂性,他们往往侧重于“运行”的重要性——而不是进行根本原因分析,采取预防问题的纠正措施。日常业绩指标致使主管不断的为流程的失败去救火,例如运输问题和机械故障。对员工或监事的标准作业几乎没有重视。
开始阶段,我们的努力集中在对该快速增长的企业财务状况影响最大的区域。新设施的主要问题是成本浪费。每天工厂平均损失2200公斤调味成分。 因为这个过程是密封的,机器操作工看不到废料。但在会计报表中出现每月超过5万美元的差异。
该公司的其他分部正在努力的保持高于65%的效率水平。 正如在许多企业中的情况一样,问题会出现并被改正,然后很快再次出现。其根本原因尚不清楚,因此从未完全解决。
为进一步发展奠定基础
2014年,TBM的工作开始于培训和重新引入精益管理工具和方法。当时这两个分部都没有任何工作人员专心致志地持续改善。为了支持企业文化的培养和持续进步,我们确定了可持续改善项目的现有员工,之后2015年为支持这两个分部工作聘请了新的CI计划管理人员。
通过员工访谈和数据分析,我们制作了关于一系列问题的潜在解决方案。与私募基金的代表共同合作,初步评估确定了三大CI协调中心:
- 领导层的标准工作
- 八步问题解决方法和A3报告
- 结构化分层的日常管理系统
让各个层级的管理者参与,为他们设计培训材料,介绍问题解决的概念和流程步骤,然后将其应用于现实问题。例如,每个培训参与者从最初的问题列表中选择一个,或从他们的领域中选出一个,然后通过八个步骤来创建A3来解决问题流程。
在这次培训之后,在第一个工厂,我们通过一周的改善活动来解决原材料浪费的问题。该改善团队包括来自供应商的代表,他们的参与有助于确定问题的根本原因。通过观察和分析,该团队发现容器底部出口设计了防止了大量流动的出口。就像番茄酱紧贴在一个倒置的瓶子的一边。
改善团队改变了承载角度,并创造了一些新的机械工具,将浪费减少了一半。嵌入新流程需要对机器操作员的标准工作进行修改。分层审核确保遵循规划好的步骤。同样的方法也被用于减少其他原材料的浪费改善活动。
在第二个工厂,重点是建立一个更强大的管理体系。当我们开始的时候,领导班子通常每天早上会花15-30分钟的时间来审查当前的生产状况并解决问题。会议在远离工厂车间办公区域的会议室进行。此外,轮班主管之间的切换是以特设的方式发生的,每条生产线的生产绩效并没有以最说明问题的方式来衡量。
TBM帮助实施了更加结构化的生产管理系统。具体来说,在我们的帮助下,各分区经理开始跟踪和报告SQDC(安全,质量,交付和成本)的绩效,并在每小时报告板上记录了具体问题。现场领导和区域主管在日常审查会议上讨论这些问题,会议现在设在生产车间的一个安静的房间里。这样,在必要的时候,每个人都可以方便的出来,看到现场的任何问题。可视性也加强了管理层参与改善过程,进一步激励了员工。
改变管理层的认知
随着时间的推移,每个工厂的平均生产效率提高到70%左右,这是最初的目标。工厂经理继续尝试通过跟踪设备运营效率并进一步提高正常运行时间来提高效率。结合其他业务计划,这些运营改善支持了公司持续的销售增长,并对财务状况产生了重大影响,帮助其在2015年恢复盈利并创造业绩记录。
通过在其中一家工厂实施管理系统的改变和解决问题方法的改善试点,公司管理层随后与同僚分享了实践和经验教训。公司的成功很大程度可归因于这种分享和创造学习文化的意愿。
尽管有一些初步的怀疑,管理层也愿意尝试新的方法,看看它们是否有效。他们并非是尝试几天的时间,看到没有效果就改变计划。 他们会坚持3-4周的过程变化,这足以解决关键问题,形成新的习惯,看到结果,然后再进一步调整。这种态度和方法对快速增长的初创企业或任何制造业企业仍然至关重要,对公司的销售和利润增长作出重大贡献。
除了日常库存管理实践之外,成功的战略部署还必须优化对库存具有影响的决策。
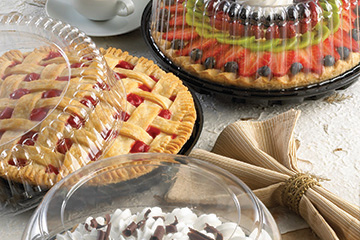
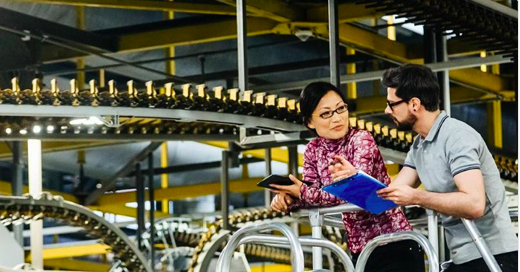