互联网的发展,社交媒体的评论,是消费品行业质量概念的颠覆 — 即使是已经达到最高质量标准的公司。
TBM曾经服务的一家客户,超力包装,就曾经碰到过类似情形。超力包装为多家世界著名的食品饮料行业的公司提供外包装产品,当时少数消费者对产品外包装的抱怨引起了一家著名客户的关注。
“个体的消费者现在可以迅速的发表产品体验,”
超力全球流程工程师Martin P. Malloy 解释说
“超力和它的客户对于现场的任何缺陷非常敏感,即使缺陷率非常低,因为抱怨会通过数个网络社区引起指数级的信息爆炸。” 超力的“盒装内袋包装”包装系统对于商业和零售食品饮料产品是流行的。公司一年生产9500万个系统。品牌客户1年收到约30个关于盒装泄露的抱怨。
即使缺陷在3000万机会中发生(6.25西格玛水 平),客户需要快速的解决问题因为抱怨张贴会被在社交媒体网站上,然后迅速传播,对品牌的影响,和客户的忠诚度产生非常不好的影响。
即使抱怨反映了质量问题的洞察力而不是基于通常认知统计参数的实际质量问题,超力的客户需要快速的解决问题预防任何负面的评论。 超力已经实施精益实践,但需要更加深入的改善,所以引入TBM帮助他们从根本上更快速更有效果的实施改善和变革。
精益西格玛工具识别根本原因快速改善
TBM同时运用六西格玛问题解决和精益的快速流程改进方法,整合 DMIAC流程 (Define定义- Measure测量-Analyze分析- Improve改进-Control控制)。最终的工具对于有着许多变异源且流程拥有者需要快速取得结果的项目而言是完美的。精益西格玛改善能够缩短从定义到控制的时间,从几个月缩短为几周。
“精益西格玛改善对于食品饮料行业而言是很好的工具,因为它们可以快速见效,
而且不得不做很多的测试,测试发生时有很多的变异存在,”
Beth Morrison, TBM咨询集团高级咨询师和盒装内袋包装项目导师说道。
西格玛改善将DMAIC问题解决方法的精度与精益改善流程的改进活动的速度相结合。在西格玛改善项目过程中,跨职能团队通常在定义和测量费时一周;用4到6周时间收集数据;1周分析和改进;1周进行控制。通常DMAIC 方法论需 要耗时6月到8月。
超力第一步是数据分析。为客户生产最多产品的工厂成 为实验场所。那儿进行的改善活动能够被借鉴到其他工 厂类似产品上。 作为六西格玛改善流程的一部分,试验 工厂的跨部门团队开始寻找根本原因的工作。
应用退回产品、头脑风暴、失效模式与效应分析的结合, 团队将重点快速集中在单个注塑部件上。他们通过假设 检验发现模具参数的差异将导致部件不仅有工厂与工厂 之间变异,而且同一工厂不同批次之间也有差异的行为 特征。
团队面临着以下问题:部件的哪些特征应当测量,从而 可以显示对整个系统的表现?
按照DMAIC流程,团队建立了可以预测部件未来表现的 可重复的测量系统。同时团队也开始调查潜在的变异源 以确定影响生产部件一致性的参数。
实验设计定义优化模具设置
团队使用实验设计(DOE),一种统计方法同时测试了 多个变量,以确定生产流程中哪些需要被调整以减少变 异。经过一轮实验后,团队能够确定最优设置来生产符 合要求的部件。
正如开始计划的那样,团队通过应用最优设置在其他工厂 复制改进活动—但是最初的结果却不容乐观
团队调查后意识到他们不得不后退一步:取代复制最优注塑设置,他们需要复制问题解决技巧。在每个工厂设备和模具的差异导致了流程的巨大变异,实验设计需要在每一个工厂进行复制,产生的最优设备设置对于每个工厂都是独一无二的。
一旦实验设计的标准化工作建立起来,将在不同工厂推广 开来。今天,每个工厂,使用不同的模具和不同的设备, 也能够生产出有着严格公差带的产品。
遵守流程,使用跨部门团队,确保团队进行测量会反映到 未来为客户生产出更好的产品。客户抱怨也随之停止了。
“西格玛改善方法被认为是一种笨重而缓慢的流程,但我 认为这是由于起初对于资源的大规模投入所致,” Malloy 说。 “最终,超力解决了这个在我们和客户端多年来一直 头痛的问题。我们用数月的时间就完成了任务。”
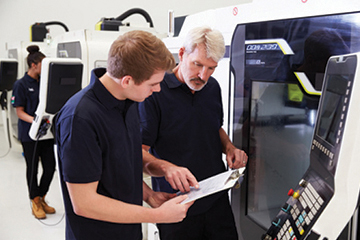
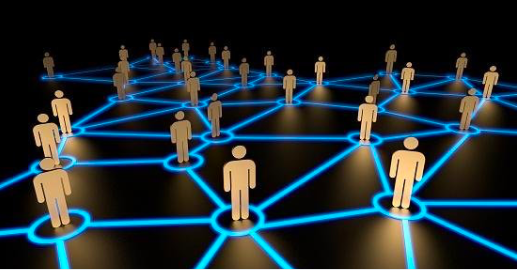