层层递进,全员改善,提升企业管理水平
从最初的概念普及和推广,到通过精益改善降低运作成本、减少浪费,再到改善价值链整体效率, 直至在公司上下形成浓厚的改善文化。短短的三年里,欧文斯科宁在 TBM 指导下取得了无数成 功的改善经验,也体味了改善给企业管理带来的诸多益处。
全美财富 500 强企业之一的欧文斯科宁是世界建筑材料和玻璃纤维复合材 料领域的领先者。自二十世纪八十年代进入中国市场以来,欧文斯科宁已分别在 广州、上海、南京、天津、拥有 4 家建筑材料工厂和 1 家复合材料工厂。其亚太 区总部位于中国上海,在包括中国、日本、韩国、东南亚、澳大利亚、新西兰和 印度在内的各个国家、地区都设有工厂、销售办事处及覆盖广泛的分销网络。2005 年,公司又在上海成立了亚太区科学技术中心。
精益管理最初是四、五年前在欧文斯科宁的美国总部通过与 TBM 公司的合 作开始推行实施的。由于获得了不小的成功,美国总部遂与亚太区沟通,希望将 总部推行精益管理的成功经验向亚太区推广开来。在聆听考察了美国总部推行的 精益管理和持续改善(CI)等方面的成功做法和经验之后,欧文斯科宁亚太区的 精益管理也进入了正式计划与实施。
改善之初
应该说,欧文斯科宁亚太区的精益改善最初是自上而下的,也就是听取学习 了总部的成功经验与对实施精益的倡导,首先对公司精英管理层进行教育普及, 之后再由管理层逐步传递,带动下属团队负责人乃至基层一线生产人员和各职能 管理部门把精益管理推广开来,最终在整个公司内部形成精益管理和持续改善的 文化。公司对精益改善这个任务的定位是“从下到上,全员参与,形成精益改善 的公司文化,成为人才培养的先锋”。
据公司改善办公室负责人陆中一介绍,在亚太区正式开始实施精益改善之前, 公司基本上没有接触过精益。除了个别公司领导骨干参加过一些西格玛的培训, 或者个别来自汽车行业的员工曾经接触过 TPM、5S 以外,几乎所有员工都对精 益不甚了解或者认识非常模糊。
树立改善目标,制订行动计划
针对上述情况,公司与 TBM 讨论之后很快设立了如下四个层面的主要目的: 首先,在领导骨干层(如厂长、部门经理)进行普及培训,让这些人先了解 精益的概念; 其次,随着本地市场竞争的不断加剧,企业降低运作成本的需要越来越迫切, 因此将通过精益管理改善项目来帮助减少浪费,提高成本效益; 第三,以公司骨干层为起点,逐层传递,将精益的精髓思想方法与实践经验 在整个公司内传播开来,逐步形成精益管理和持续改善的文化与氛围; 第四,运用精益改善工具,从订单、生产、运输等各个环节对公司整个价值 链的效率进行系统改善,从而提升公司的整体管理水平。
围绕上述目标,相应的行动计划也随之出炉:
全员培训——首先对公司管理层骨干进行专题培训,使其了解精益和改善的 基本概念。之后分期分批在全体员工中进行精益改善培训,确保每位员工每年至少参加一次相关内容的培训。
全员参与——公司改善办公室与 TBM 公司携手,对亚太区各工厂和职能部 门的价值链进行评估,找出存在改进空间的各个方面,确立相应的改善项目 数目并下达到每个工厂和职能部门;工厂和职能部门则各自建立全职的持续 改善团队,自行定义具体改善项目并加以实施。
竞赛评比——亚太区每年举行年度最佳改善项目评比。
Learning by Doing(实践出真知)
TBM 在帮助企业推广精益改善时有一个非常突出的思想理念:Learning by Doing,就是不把精益改善仅仅局限在理论培训的教条之中,而是将精益理论与 企业实践紧密结合,在企业的日常管理和运营中自然融入精益思想和理论,又通 过最终的改善结果反过来验证精益的思想和理论。这个理念在欧文斯科宁亚太区 的精益改善项目规划、人员配备、项目实施、人员培训和奖励机制中得到了淋漓 尽致的体现。
亚太区每个工厂每年约有 20 个左右的改善项目会付诸实施。项目的改善内 容包罗万象,比如有针对设备维护的,减能耗的,提高产量的,减少原材料损耗 的,改善叉车行驶路线的,等等。在 TBM 顾问的指导下,这些项目的规划和确 立有的是依据每年年底由部门经理和厂长对本部门或工厂的整个价值链流程所 作的评估结果,有的则是采纳了员工在日常工作的经验积累下自发提出的合理化 建议。通过上述途径,每年都会产生一些新的改善项目。
接下来的任务是确定各项目的参加实施队伍。经验丰富的 TBM 顾问在全面 了解了欧文斯科宁亚太区的组织架构和价值链运作模式以后,建议公司在项目实 施队伍的人员配备上奉行是独特的“1/3+1/3+1/3”原则——即改善项目由三 方面的人组队参加:由 1/3 懂行的专家带领 1/3 不完全懂行的项目执行者(比如 搞设备的)去执行项目,但同时有另外 1/3 完全不懂行或与改善内容无直接关系 的其它部门人员(如财务,人事等)在旁观摩学习。最后 1/3 的人参与项目的目 的,一方面是推动企业内部文化和凝聚力的形成,另一方面也能促进部门之间的 相互交流,让这些人员通过参与项目对精益改善的耳濡目染,当他们回到本职岗 位之后,也会自动自发的去帮助本部门推行精益改善或至少提出一些改善建议。 正是这样一个“1/3+1/3+1/3”的人员机制,在公司精益改善的过程中起到了 一个逐步推进,培养公司内部改善氛围的重要作用。
亚太区每个工厂大约有 100 名员工。每个改善项目大约为期一周(5 天), 每个项目约有 6-7 名员工参加。照此规模计算,亚太区每年有 80%以上的员工都 亲身参加过改善项目的实施。
除了正式的持续改善项目以外,公司每年 10 月都组织一期专门的大规模改 善训练营,培养基本人员(第一期培训对象为部门经理,第二期为工厂领班和部 门团队负责人,第三期为一线员工),每年有 25 人左右参加。训练营是全脱产的, 为期一周左右,培训师则由 TBM 的顾问担任,其培训方式是“边培训边做”— —在培训精益的各种基本概念的同时穿插一些实际的小项目——讲一个概念后 到车间去实践一下,有意识的对培训的精益工具加以应用。这些项目与跟财务数 据挂钩的正式改善项目不同,主要以培训为目的。到目前为止,这样的训练营已 经举行了三期,累计参加人数 70-80 人。今年的第四期训练营将还是针对一线员 工进行,今后针对的对象会越来越基层。 每年亚太区都会举行精益改善项目的年度评比,每个部门会提交一个自认为 实施得最好的项目参加评比,由专门的评委会(评委会成员来自各个职能部门, 如专家、技术人员、人事、财务,并邀请 TBM 顾问担任评委会主任)评选出当 年亚太区的最佳改善项目并给与一定的物质奖励,以有利于今后持续改善项目的 开展。
从被动到自觉,效果非凡
不难想象,改善推行的初期,大部分员工并非出于自觉,而是单纯听从美国 总部的倡议和被动的执行管理层布置下来的改善项目。对此,TBM 建议公司将 5S 管理巧妙的融合到办公室管理规章的制订中去,逐步变成公司上上下下的习 惯和行为模式。从开头管理层的培训,到针对基层人员结合实践的培训,到从上 到下逐步的推动,三年下来,公司已渐渐做到全员都参与到精益改善中去。
在实施改善之前,工厂中存在着环节过多、流程过长,能耗过高,人员冗余, 单位产品原材料损耗过高等各种问题。实施了各种有针对性的改善项目之后,在 确保产品质量符合客户要求前提下,单位产品生产能耗大大降低,仓库周转加快、 库存减少,设备维修费用也大大减少。在最初的两、三年里,每年节省运营成本 达 300-400 万美元。生产价值链效率的明显提高使公司上下对精益改善的效果信 心倍增。
不仅生产成本得到了节省,公司的员工也着实在持续不断的精益培训和项目 实施中普遍得到了培养。比如,亚太区实施了很多维修方面的 TPM 项目,原本 设备的维修保养是由设备科和工程部专门负责的,如今通过全员培训,当班的一 线员工也共同参与到设备维护工作中,设备检修费用大大减少,也使工厂绝大多 数员工都普遍意识到设备维护是每个人的职责。
通过培训,不仅整个公司对 LEAN 和西格玛的基本概念有了普遍了解,在员 工的日常交流中也多了不少共同语言,比如:西格玛,DOE,5S,TPM,节奏, 自动化,及时生产等。而每个部门在制定各自的关键绩效指标(KPI)时会有意 识的运用一些精益工具来进行辅助。
另外,员工在日常工作中也会有意识的应用一些精益工具来解决一些日常问 题,比如研发设计人员在进行产品设计或老产品效能改善时,会有意识的运用培 训中学到的实验设计(DOE)的方法,使得设计出来的产品/解决方案更加出色, 开发时间也会有相应缩短。
除此以外,一些细小的方面也逐步显现出精益改善的踪影:比如办公室环境, 员工着装,思想意识、行为举止等都更加规范了。可以看出,精益改善已不仅仅 以节省成本为目的,当改善实施到一定程度,更多的是提高一个公司的管理水平。
改善无止境
正如陆中一先生所言,欧文斯科宁的“改善之路”还远远没有结束。
除了全员普及的改善培训以外,欧文斯科宁每年还会开设一期六西格玛/绿 带/黑带班,旨在培养管理层精英,为后备管理人员储备服务。
2012 年将举行一期厂长培训班,培训的课程水准会更高,旨在提升厂长这 一层的管理水平。
任何改善,实施了一段时间后一定会遇到瓶颈,如何在现有的成绩基础上进 一步突破,在未来取得更大的进步?欧文斯科宁相信,借鉴一些其它公司的成功 经验,可以拓宽未来改善的思路,提升每年改善项目的创新程度。今后,公司将 邀请 TBM 介绍其外部客户公司的先进改善经验,组织公司高层前往参观学习交 流,寻找更高的改善目标。
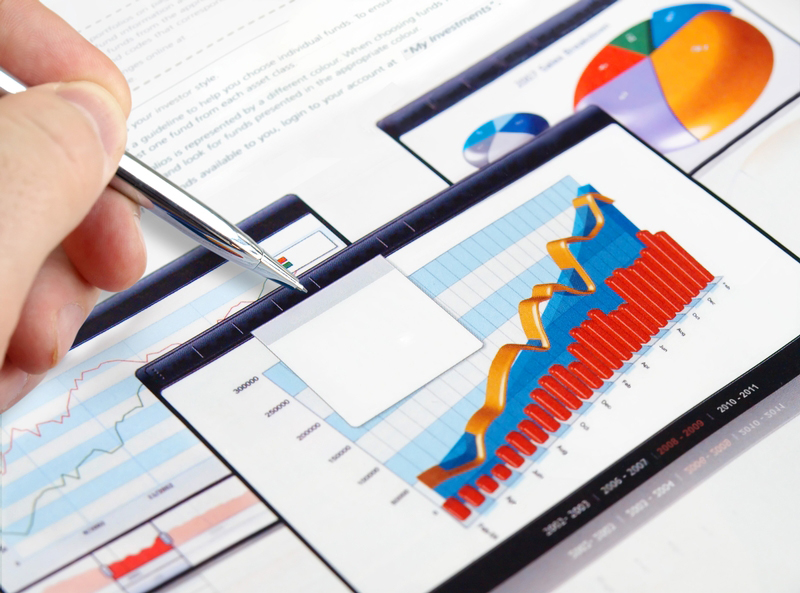
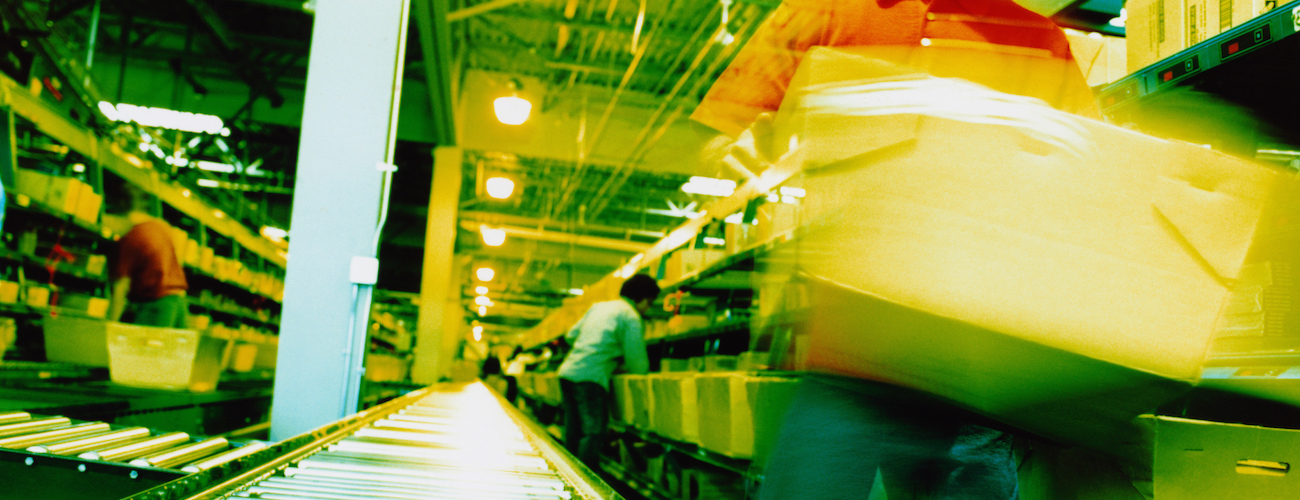